Maytag Electric Dryer Motor Stops Running After Start Switch is Released
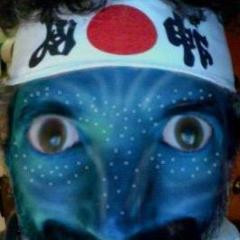
Samurai Appliance Repair Man in Tech Talk
FAQs | Repair Videos | Academy | Newsletter | Contact
Pearls of appliance repair wisdom from the Appliantology Forums
Samurai Appliance Repair Man in Tech Talk